“We want to develop the energy-self-sufficient factory”
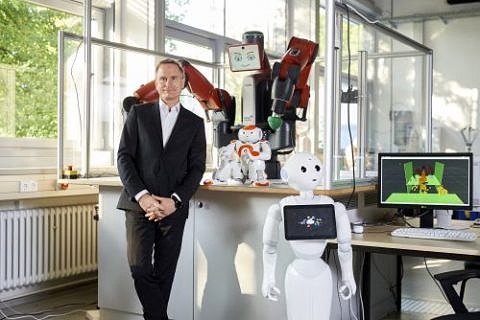
An interview with Prof. Dr. Jörg Franke on the Green Factory Bavaria project
The Green Factory Bavaria project was launched seven years ago. Twelve research institutes and more than one hundred companies jointly pursued the ambitious goal of minimising resource consumption in production. Prof. Dr. Jörg Franke from the Institute of Factory Automation and Production Systems (FAPS) at FAU coordinated the collaborative project. We asked him about the most important results of the Green Factory Bavaria.
Professor Franke, the Green Factory Bavaria project was launched in 2013, what was the initial goal of the project?
The German federal government’s decisions for a renewable energy supply and the withdrawal from nuclear energy, which will lead to the shutdown of the remaining four Bavarian nuclear power plants by 2022, presents us with enormous challenges. This has a particular impact on the manufacturing industry which consumes almost half of the electrical energy supply in Germany. The potential energy savings are immense at up to 30 percent. In addition to contributing to the energy reform, protecting resources is also a strategic and competitive factor for companies, as customers, employees and society develop a growing awareness of sustainable economy. The Green Factory Bavaria was created to support Bavarian companies in reducing their resource consumption and to develop a concept for the energy-self-sufficient factory.
What strategy did you follow to achieve this goal?
We have pursued two main lines of action: firstly, the transfer of applied research to industry and, secondly knowledge transfer between companies. Ten universities and two Fraunhofer institutes, together with more than one hundred companies from all over Bavaria, have developed technical solutions and methodological approaches to reduce resource consumption. Green Factories have been set up and expanded as demonstration, learning and research platforms for energy-efficient production. Specific technology priorities were set at each site and the results made available to other companies.
There are many ways of saving energy. What did the projects focus on?
Around 80 individual projects were launched as part of the Green Factory Bavaria. The spectrum is incredibly broad: a selection of projects dealt with production management, optimised machine scheduling and maintenance to avoid idling phases and downtime, shorter distances for transport vehicles and robots or the elimination of redundant IT structures. Other project groups worked to improve the properties of materials and joints – smoother and harder surfaces to reduce friction losses, for example, more robust switching joints that do not require energy-intensive thermal shock testing, and shaping and welding processes that save both material and energy. We knew from the start that the energy-self-sufficient factory would involve a number of complex solutions rather than an easy answer.
Which of these projects were particularly successful?
I would describe the entire project as a great success. 60 completed individual projects with a total of 61 funded full-time positions, 23 doctoral degrees, 236 scientific publications and 324 theses – these alone are already impressive figures. In terms of operational energy efficiency, some of the results were outstanding: In the E|UROPA project, up to 72 percent of the energy required was saved by optimising the electrodes during hot crimping, and 86 percent savings compared to conventional processes could also be achieved by inductive heating. In the E|Vertech project, an ultrasonic welding process was developed that reduces the energy consumption of joining processes in electrical machinery construction by 90 percent. These are incredible results, and energy saving potentials have also been discovered in almost all other projects, many of which have already been implemented to some extent despite the relatively short duration of the research.
Were there areas where your expectations have not been met?
In the course of the project work, we found that both the potential of energy savings and their implementation are highly industry- and process-dependent. For example, an energy saving potential of about 15 percent could be identified in forming technology and a third of this could be implemented directly. Logistics showed a potential of around 80 percent, of which a quarter could be leveraged immediately. The processing of plastic and lightweight construction materials proved to be significantly more complex: although a potential of almost 50 percent was identified here, only two percent could be implemented directly. This shows the extent of the research needed to develop creative measures.
The collaborative project was funded until the end of 2018. What is planned for the future of this project?
Thanks to the intensive networking of the twelve participating research institutions and more than one hundred industrial partners, Green Factory Bavaria was a catalyst for sustainable research cooperation throughout Bavaria. The financial participation of companies with a total of more than 10 million euros in the projects also clearly demonstrated the importance of sustainability and energy efficiency in industry. It was clear from the start that the project would only be the starting point for further research and development. Since then, many new projects that originated from the Green Factory project have been launched at FAU and FAPS in particular. What is also very important to us is that the collaborative project not only enabled us to sustainably strengthen cooperation between science and industry, but also enabled us to contribute to developing networks with industrial partners. In times of increasing globalisation and opening up of international markets, this pooling of industrial expertise can become a decisive competitive advantage for Bavarian companies.
Further information
Prof. Dr. Jörg Franke
joerg.franke@faps.fau.de